Manufacturing operations face unprecedented challenges in maintaining equipment reliability while maximizing productivity and controlling costs. Traditional reactive maintenance approaches are no longer sufficient in today’s competitive landscape. AI predictive maintenance has emerged as a transformative solution that revolutionizes how manufacturers approach equipment management and operational efficiency.
The global AI-based predictive maintenance market demonstrates remarkable growth, expanding from USD 840.09 million in 2024 to USD 939.73 million in 2025, with projections reaching USD 1.69 billion by 2030. This explosive growth reflects the proven value that artificial intelligence brings to manufacturing technology and equipment monitoring systems.
Modern manufacturing facilities generate vast amounts of data from sensors, machinery, and production systems. AI predictive maintenance harnesses this data to identify patterns, predict failures, and optimize maintenance schedules before costly breakdowns occur. This proactive approach transforms maintenance from a cost center into a strategic advantage that drives operational excellence.
Understanding how to implement and optimize AI predictive maintenance is crucial for manufacturers seeking to remain competitive in the Industry 4.0 era. This comprehensive guide explores the technologies, strategies, and best practices that enable successful deployment of AI-powered maintenance automation systems across diverse manufacturing environments.
Understanding AI Predictive Maintenance in Manufacturing
The Evolution from Reactive to Predictive Maintenance
Traditional maintenance strategies have evolved through distinct phases, each offering different levels of efficiency and cost-effectiveness. Reactive maintenance, the most basic approach, addresses equipment failures after they occur, resulting in unplanned downtime, emergency repairs, and significant production losses.
Preventive maintenance improved upon reactive strategies by scheduling regular maintenance activities based on time intervals or usage metrics. While this approach reduces unexpected failures, it often leads to unnecessary maintenance activities and component replacements, increasing costs without optimizing equipment performance.
AI predictive maintenance represents the next evolutionary step, using advanced analytics and machine learning to predict when equipment requires maintenance based on actual condition rather than predetermined schedules. This approach maximizes equipment uptime while minimizing maintenance costs and resource waste.
The transition to predictive maintenance enables manufacturers to shift from cost-based maintenance decisions to value-based strategies that optimize overall equipment effectiveness (OEE) and support strategic business objectives.
Core Components of AI Predictive Maintenance Systems
Modern AI predictive maintenance systems integrate multiple technologies to create comprehensive equipment monitoring and analysis capabilities. Internet of Things (IoT) sensors serve as the foundation, collecting real-time data about equipment performance, environmental conditions, and operational parameters.
Machine learning algorithms analyze sensor data to identify patterns, anomalies, and trends that indicate potential equipment issues. These algorithms continuously learn from historical data and operational experiences, improving their predictive accuracy over time.
Data analytics platforms process and visualize information from multiple sources, providing actionable insights that maintenance teams can use to make informed decisions. These platforms often include dashboards, alert systems, and reporting tools that streamline maintenance management workflows.
Edge computing capabilities enable real-time processing and decision-making at the equipment level, reducing latency and enabling immediate responses to critical conditions. This distributed processing approach ensures that predictive maintenance systems can operate effectively even in environments with limited connectivity.
Industrial AI Applications Across Manufacturing Sectors
AI predictive maintenance applications span diverse manufacturing industries, each with unique requirements and challenges. In semiconductor manufacturing, AI has been employed to analyse sensor data, enabling companies to prevent expensive downtime by predicting issues in precision machinery.
Automotive manufacturing utilizes AI predictive maintenance for robotic assembly lines, painting systems, and quality control equipment. The complex automation systems in automotive plants generate substantial data streams that AI algorithms can analyze to optimize production efficiency and equipment reliability.
Chemical and petrochemical industries leverage AI predictive maintenance for process equipment, pumps, compressors, and heat exchangers. The critical nature of these systems requires highly accurate predictions to prevent safety incidents and environmental hazards.
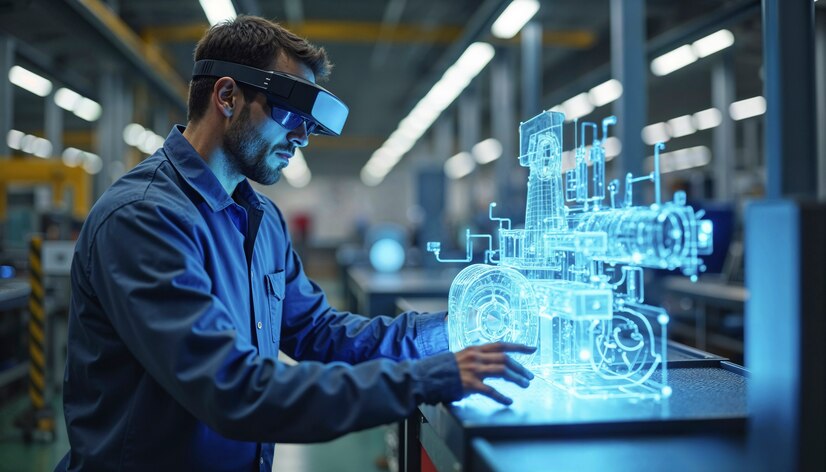
Food and beverage manufacturing applies AI predictive maintenance to packaging equipment, conveyor systems, and refrigeration units. The industry’s strict hygiene and quality requirements make predictive maintenance essential for maintaining product safety and regulatory compliance.
IoT Sensors and Data Collection Systems
Smart Sensor Technologies for Equipment Monitoring
The effectiveness of AI predictive maintenance depends heavily on comprehensive data collection from various sensor technologies. Vibration sensors detect mechanical issues like bearing wear, misalignment, and imbalance in rotating equipment, providing early warning signs of potential failures.
Temperature sensors monitor equipment operating conditions and identify overheating issues that could lead to component failure or safety hazards. These sensors are particularly valuable for electrical systems, motors, and heat-generating processes.
Acoustic sensors detect unusual sounds and noise patterns that indicate equipment problems. Advanced acoustic monitoring can identify issues like cavitation in pumps, gear tooth damage, or bearing deterioration through sophisticated signal processing techniques.
Pressure and flow sensors monitor fluid systems and identify blockages, leaks, or pump performance issues. These sensors are essential for hydraulic systems, compressed air systems, and process fluid management.
Data Acquisition and Processing Architecture
Modern manufacturing environments require robust data acquisition systems that can handle multiple sensor types, data formats, and communication protocols. Industrial IoT gateways serve as collection points that aggregate sensor data and transmit it to centralized processing systems.
Edge computing devices process sensor data locally, enabling real-time analysis and immediate response to critical conditions. This distributed processing approach reduces network bandwidth requirements and ensures system responsiveness even during connectivity issues.
Cloud-based data platforms provide scalable storage and processing capabilities for large-scale predictive maintenance implementations. These platforms can handle massive data volumes from multiple facilities and support advanced analytics and machine learning operations.
Data integration systems ensure that predictive maintenance platforms can access information from existing manufacturing execution systems (MES), enterprise resource planning (ERP) systems, and other operational technologies. This integration provides context for maintenance decisions and supports comprehensive operational optimization.
Wireless and Wired Communication Solutions
Communication infrastructure plays a critical role in predictive maintenance system performance and reliability. Wireless technologies like Wi-Fi, cellular networks, and industrial wireless protocols enable flexible sensor deployment without extensive cabling requirements.
Low-power wide-area networks (LPWAN) technologies such as LoRaWAN and NB-IoT support long-range, battery-powered sensors that can operate for years without maintenance. These technologies are particularly valuable for remote or difficult-to-access equipment.
Industrial Ethernet networks provide high-speed, reliable communication for mission-critical applications. These wired networks offer deterministic performance and robust security features essential for industrial environments.
5G technology promises to revolutionize industrial communications by providing ultra-low latency, high bandwidth, and massive device connectivity capabilities. 5G technology and expansion into new industries are driving the growth of the AI in Predictive Maintenance Market.
Machine Learning Algorithms for Predictive Analytics
Supervised Learning for Failure Prediction
Supervised learning algorithms form the foundation of many predictive maintenance applications by learning from historical data that includes both equipment conditions and known failure outcomes. These algorithms can identify patterns that precede equipment failures and predict when similar conditions might lead to future problems.
Classification algorithms determine whether equipment is operating normally or showing signs of potential failure. These binary or multi-class classification systems can categorize equipment conditions and trigger appropriate maintenance actions based on predicted failure modes.
Regression algorithms predict continuous variables like remaining useful life (RUL) or time to failure. These predictions enable maintenance teams to plan interventions with greater precision and optimize resource allocation across multiple assets.
Support vector machines (SVM) excel at identifying complex patterns in high-dimensional sensor data. These algorithms can detect subtle changes in equipment behavior that might indicate developing problems before they become apparent through traditional monitoring methods.
Unsupervised Learning for Anomaly Detection
Unsupervised learning algorithms identify unusual patterns or anomalies in equipment behavior without requiring labeled training data. These approaches are particularly valuable for detecting novel failure modes that weren’t present in historical data.
Clustering algorithms group similar operating conditions and identify outliers that might indicate equipment problems. These techniques can reveal previously unknown relationships between operating parameters and equipment health.
Principal component analysis (PCA) reduces the dimensionality of sensor data while preserving important information about equipment behavior. This technique helps identify the most significant factors affecting equipment performance and simplifies monitoring systems.
Autoencoders, a type of neural network, learn to reconstruct normal equipment behavior and identify anomalies based on reconstruction errors. These deep learning approaches can detect complex, non-linear patterns in equipment data.
Deep Learning and Neural Networks
Deep learning algorithms excel at processing complex, multi-dimensional data from modern manufacturing equipment. Convolutional neural networks (CNNs) analyze image data from thermal cameras and visual inspection systems to identify equipment problems.
Recurrent neural networks (RNNs) and long short-term memory (LSTM) networks process time-series sensor data to identify temporal patterns and trends. These algorithms can capture long-term dependencies in equipment behavior that traditional methods might miss.
Transformer architectures, originally developed for natural language processing, are being adapted for industrial time-series analysis. These models can identify complex relationships between different sensor signals and operational parameters.
Generative adversarial networks (GANs) create synthetic training data for rare failure modes, addressing the challenge of limited failure data in industrial applications. This approach improves model training and enhances prediction accuracy for uncommon but critical failure scenarios.
Equipment Health Monitoring Systems
Real-Time Condition Monitoring
Real-time condition monitoring systems provide continuous visibility into equipment health and performance. These systems process sensor data in real-time to identify immediate concerns and track long-term trends that indicate equipment degradation.
Dashboard interfaces present equipment status information in intuitive formats that enable operators and maintenance technicians to quickly assess conditions and identify priorities. Color-coded indicators, trend charts, and alert systems streamline decision-making processes.
Automated alert systems notify relevant personnel when equipment conditions exceed predetermined thresholds or when predictive models indicate potential problems. These alerts can be customized based on equipment criticality, failure modes, and organizational workflows.
Mobile applications enable field technicians to access equipment health information from anywhere in the facility. These apps can display real-time data, historical trends, and maintenance recommendations directly on smartphones or tablets.
Digital Twin Technology Integration
Digital twin technology creates virtual representations of physical equipment that mirror real-world conditions and behavior. These digital models enable advanced simulation and analysis capabilities that enhance predictive maintenance effectiveness.
Physics-based models incorporate engineering principles and equipment specifications to simulate equipment behavior under various operating conditions. These models provide insights into failure mechanisms and help validate predictive maintenance recommendations.
Data-driven digital twins learn from operational data to continuously improve their accuracy and predictive capabilities. Machine learning algorithms update these models as new data becomes available, ensuring they remain aligned with actual equipment behavior.
Hybrid digital twins combine physics-based modeling with data-driven approaches to leverage the strengths of both methodologies. These comprehensive models provide the most accurate predictions and support sophisticated maintenance optimization strategies.
Prognostic Health Management
Prognostic health management (PHM) systems integrate multiple data sources and analytical techniques to provide comprehensive equipment health assessments. These systems go beyond simple condition monitoring to predict future equipment states and optimize maintenance decisions.
Remaining useful life (RUL) predictions help maintenance teams plan interventions at optimal times, balancing equipment reliability with maintenance costs. Accurate RUL estimates enable better resource planning and inventory management.
Health index calculations combine multiple condition indicators into single metrics that represent overall equipment health. These simplified indicators make it easier for operators and managers to understand equipment status and prioritize maintenance activities.
Risk assessment models evaluate the probability and consequences of equipment failures to support maintenance decision-making. These models consider factors like production impact, safety implications, and repair costs to optimize maintenance strategies.
Maintenance Automation and Workflow Optimization
Automated Work Order Generation
AI predictive maintenance systems can automatically generate work orders when equipment conditions warrant maintenance intervention. These automated systems ensure that maintenance activities are initiated promptly and reduce the risk of overlooking critical maintenance needs.
Intelligent work order systems include detailed information about predicted problems, recommended actions, required parts, and estimated labor requirements. This comprehensive information helps maintenance teams prepare effectively and complete work efficiently.
Integration with enterprise asset management (EAM) and computerized maintenance management systems (CMMS) ensures that automated work orders flow seamlessly into existing maintenance workflows. This integration maintains organizational processes while adding predictive capabilities.
Priority-based scheduling algorithms consider equipment criticality, production schedules, and resource availability to optimize maintenance timing. These systems balance competing demands and ensure that critical equipment receives appropriate attention.
Resource Planning and Inventory Management
Predictive maintenance systems support improved resource planning by providing advance notice of maintenance requirements. This predictive capability enables better coordination of maintenance activities and more efficient use of human resources.
Spare parts optimization leverages failure predictions to maintain appropriate inventory levels without excessive carrying costs. AI algorithms can predict parts demand and optimize ordering schedules to ensure availability when needed.
Maintenance scheduling optimization considers multiple factors including equipment priorities, technician skills, parts availability, and production schedules. These comprehensive scheduling systems maximize maintenance efficiency while minimizing production disruption.
Vendor management systems coordinate with external service providers based on predictive maintenance insights. These systems can automatically schedule vendor services or request quotes for specialized maintenance work.
Integration with Enterprise Systems
Successful predictive maintenance implementations require seamless integration with existing enterprise systems. Enterprise resource planning (ERP) integration ensures that maintenance activities are coordinated with production planning, financial management, and procurement processes.
Manufacturing execution system (MES) integration provides real-time production context for maintenance decisions. This integration enables maintenance teams to understand production impacts and coordinate activities with operational requirements.
Quality management system integration helps identify relationships between equipment condition and product quality. This integration supports proactive quality management and helps prevent quality issues before they affect production.
Business intelligence platforms aggregate predictive maintenance data with other operational metrics to provide comprehensive performance insights. These integrated dashboards support strategic decision-making and continuous improvement initiatives.
Implementation Strategies and Best Practices
Pilot Project Planning and Execution
Successful AI predictive maintenance implementations typically begin with carefully planned pilot projects that demonstrate value and build organizational capabilities. Pilot projects should focus on equipment that offers significant potential benefits while managing implementation complexity and risk.
Equipment selection criteria for pilot projects include high criticality, frequent maintenance requirements, availability of historical data, and sensor accessibility. Starting with equipment that meets these criteria increases the likelihood of pilot project success and provides compelling results for broader deployment.
Success metrics for pilot projects should include both technical performance indicators and business value measures. Technical metrics might include prediction accuracy and false alarm rates, while business metrics could include maintenance cost reduction and uptime improvement.
Stakeholder engagement throughout the pilot project ensures that all affected parties understand the technology and its implications. Regular communication and training help build support for broader implementation and address concerns proactively.
Data Strategy and Infrastructure Development
Effective data strategy forms the foundation of successful predictive maintenance implementations. Organizations must develop comprehensive approaches to data collection, storage, processing, and governance that support both current needs and future expansion.
Data quality management ensures that predictive maintenance systems have access to accurate, complete, and timely information. Poor data quality can undermine predictive model performance and lead to incorrect maintenance decisions.
Data architecture design must consider factors like data volume, processing requirements, security needs, and integration requirements. Scalable architectures support growth and evolution as predictive maintenance programs mature.
Cybersecurity considerations are critical for industrial IoT implementations. Robust security frameworks protect sensitive operational data and prevent cyber threats that could disrupt manufacturing operations.
Change Management and Training
Organizational change management is essential for successful AI predictive maintenance adoption. These systems often require significant changes to maintenance processes, roles, and responsibilities that must be managed carefully to ensure acceptance and effectiveness.
Training programs should address both technical skills and operational procedures. Maintenance technicians need to understand how to interpret predictive maintenance insights and integrate them with traditional maintenance practices.
Performance measurement systems should track both technology performance and organizational adoption metrics. Understanding how well teams are utilizing predictive maintenance capabilities helps identify areas for improvement and additional support needs.
Continuous improvement processes ensure that predictive maintenance systems evolve and improve over time. Regular reviews of system performance, user feedback, and business results support ongoing optimization and value enhancement.
Industry-Specific Applications and Case Studies
Automotive Manufacturing Excellence
The automotive industry represents one of the most advanced adopters of AI predictive maintenance due to its complex automation systems and strict quality requirements. Robotic assembly lines utilize predictive maintenance to prevent costly production disruptions and maintain precise manufacturing tolerances.
Paint shop operations benefit significantly from predictive maintenance systems that monitor spray booth conditions, paint supply systems, and environmental controls. Predictive maintenance helps prevent paint defects and ensures consistent finish quality across production runs.
Body shop welding operations use AI predictive maintenance to monitor welding robot performance, electrode wear, and weld quality indicators. These systems prevent weld defects and reduce the need for costly rework and quality inspections.
Powertrain manufacturing applies predictive maintenance to machining centers, assembly equipment, and testing systems. The precision requirements of engine and transmission manufacturing make predictive maintenance essential for maintaining product quality and production efficiency.
Chemical and Process Industries
Chemical manufacturing presents unique challenges for predictive maintenance due to harsh operating environments, safety requirements, and process complexity. AI predictive maintenance systems must operate reliably in environments with extreme temperatures, corrosive chemicals, and explosive atmospheres.
Pump and compressor monitoring represents a critical application area where predictive maintenance prevents catastrophic failures that could result in safety incidents or environmental releases. Advanced analytics can detect cavitation, impeller damage, and bearing problems before they lead to equipment failure.
Heat exchanger monitoring uses AI to detect fouling, corrosion, and thermal performance degradation. Predictive maintenance systems can optimize cleaning schedules and prevent efficiency losses that increase energy costs.
Reactor and vessel monitoring applies predictive maintenance to critical process equipment where failures could have severe safety and environmental consequences. These applications require highly reliable prediction systems with extensive validation and safety interlocks.
Food and Beverage Production
Food and beverage manufacturing requires predictive maintenance systems that operate in sanitary environments while maintaining strict hygiene standards. AI systems must account for frequent cleaning cycles and sanitization procedures that can affect sensor performance.
Packaging equipment represents a major application area where predictive maintenance prevents production delays and product quality issues. High-speed packaging lines require precise timing and coordination that predictive maintenance systems help maintain.
Refrigeration and cooling systems benefit from predictive maintenance that prevents temperature excursions that could affect product safety and quality. These systems monitor compressor performance, refrigerant levels, and heat exchanger efficiency.
Conveyor systems use predictive maintenance to prevent belt failures, bearing problems, and motor issues that could disrupt production flow. Chain conveyors, belt conveyors, and pneumatic systems all benefit from AI-powered condition monitoring.
Cost-Benefit Analysis and ROI Measurement
Financial Impact Assessment
Implementing AI predictive maintenance requires significant upfront investment in sensors, software, and infrastructure. AI adoption requires a large upfront investment in technology and infrastructure, which can be a barrier, especially for smaller companies. However, the financial benefits often justify these investments through reduced maintenance costs, improved equipment reliability, and increased production efficiency.
Direct cost savings from predictive maintenance include reduced emergency repairs, lower parts inventory costs, and decreased maintenance labor requirements. Predictive maintenance can reduce downtime by identifying equipment and systems that are not running optimally, flagging potential problems early on, and increases production by keeping equipment operational.
Indirect benefits include improved product quality, reduced waste, and enhanced safety performance. These benefits can be substantial but may be more difficult to quantify accurately. Organizations should develop comprehensive measurement frameworks that capture both direct and indirect value.
Production impact assessment considers the value of avoided downtime and improved equipment availability. In high-value production environments, even small improvements in equipment uptime can generate significant financial returns.
Return on Investment Calculations
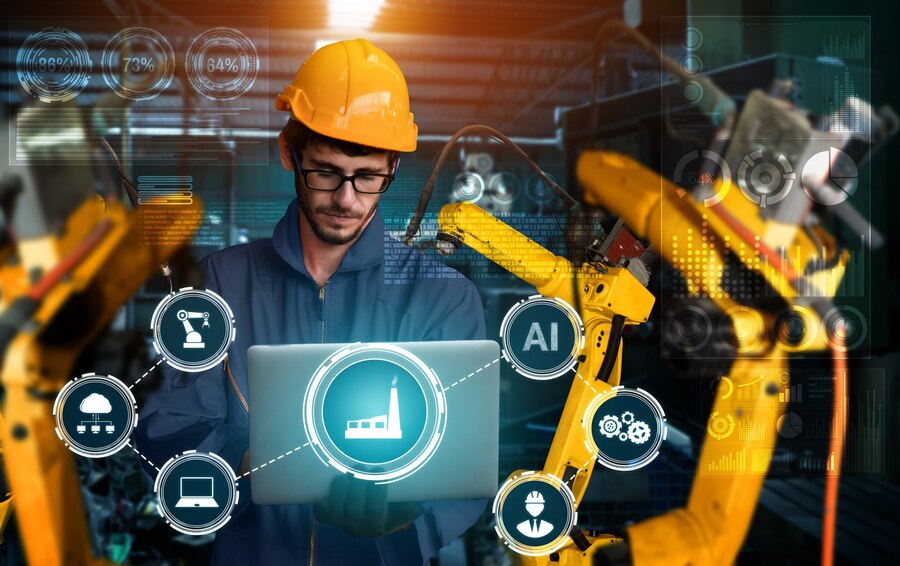
ROI calculations for AI predictive maintenance should consider both quantitative and qualitative benefits over appropriate time horizons. Typical payback periods range from 6 months to 3 years depending on equipment types, implementation scope, and operational complexity.
Maintenance cost reduction typically represents the most significant quantifiable benefit. Organizations can compare historical maintenance costs with post-implementation costs to calculate direct savings attributable to predictive maintenance.
Uptime improvement value can be calculated by multiplying avoided downtime hours by production value per hour. This calculation provides a clear metric for assessing the business impact of improved equipment reliability.
Quality improvement benefits may include reduced scrap rates, lower rework costs, and improved customer satisfaction. While these benefits can be substantial, they may require longer measurement periods to establish clear causal relationships.
Long-term Value Creation
The long-term value of AI predictive maintenance extends beyond immediate cost savings to include strategic advantages and competitive differentiation. Organizations that successfully implement predictive maintenance often achieve superior operational performance and market position.
Continuous improvement capabilities enable organizations to refine their predictive maintenance systems over time, increasing accuracy and expanding applications. This evolutionary approach ensures that investments continue to generate value throughout their lifecycle.
Data-driven insights from predictive maintenance systems support broader operational optimization initiatives. The analytical capabilities developed for predictive maintenance can be applied to energy management, production optimization, and supply chain management.
Innovation enablement represents a significant long-term benefit as predictive maintenance systems provide foundations for advanced manufacturing technologies like autonomous operations and smart factories.
Challenges and Solutions in AI Implementation
Technical Challenges and Solutions
Implementing AI predictive maintenance systems presents numerous technical challenges that organizations must address to achieve successful deployments. Data quality issues represent one of the most common challenges, as predictive models require high-quality, consistent data to generate accurate predictions.
Sensor reliability and calibration present ongoing challenges in industrial environments. Harsh conditions, electromagnetic interference, and mechanical stress can affect sensor performance and data quality. Regular calibration programs and redundant sensor strategies help address these challenges.
Algorithm selection and tuning require specialized expertise that may not be available in traditional maintenance organizations. Partnering with technology vendors or hiring data science expertise can help organizations overcome these capability gaps.
Integration complexity increases with the number of systems and data sources involved in predictive maintenance implementations. Standardized data formats and integration platforms can simplify these challenges and reduce implementation time and cost.
Organizational and Cultural Barriers
Cultural resistance to change represents a significant barrier to predictive maintenance adoption. Maintenance teams may be skeptical of AI-generated recommendations or concerned about job security. Effective change management programs address these concerns through communication, training, and involvement.
Skills gaps in data analysis and technology management can limit the effectiveness of predictive maintenance systems. Organizations must invest in training existing staff or hiring new talent with appropriate technical capabilities.
Budget constraints may limit the scope of predictive maintenance implementations. Organizations can address these constraints through phased deployments that demonstrate value and justify additional investments.
Performance measurement challenges arise when organizations lack baseline data or appropriate metrics for assessing predictive maintenance effectiveness. Establishing clear measurement frameworks before implementation helps ensure that value can be demonstrated and tracked over time.
Cybersecurity and Data Privacy Concerns
Industrial cybersecurity has become increasingly critical as manufacturing systems become more connected and digitized. Challenges such as IoT device security issues, integration with legacy systems, and high upfront costs require careful planning and scalable solutions.
Network security measures must protect predictive maintenance systems from cyber threats while maintaining operational functionality. Firewalls, intrusion detection systems, and secure communication protocols help protect against unauthorized access.
Data encryption and access controls ensure that sensitive operational data remains protected throughout the predictive maintenance system. Role-based access controls limit data access to authorized personnel based on their job responsibilities.
Vendor security assessments help ensure that third-party systems and services meet appropriate security standards. Organizations should evaluate vendor security practices and require appropriate security certifications and compliance measures.
Future Trends and Emerging Technologies
Edge Computing and Real-Time Processing
Edge computing represents a significant trend in industrial AI applications, enabling real-time processing and decision-making at the equipment level. This approach reduces latency, improves system responsiveness, and reduces bandwidth requirements for centralized processing.
Edge AI processors are becoming more powerful and cost-effective, enabling sophisticated machine learning algorithms to run locally on industrial equipment. These processors can analyze sensor data in real-time and make immediate decisions about equipment operation and maintenance needs.
Distributed intelligence architectures combine edge processing with cloud-based analytics to optimize system performance and capabilities. Edge devices handle time-critical decisions while cloud systems provide advanced analytics and machine learning model updates.
Autonomous maintenance systems represent the ultimate evolution of edge computing in predictive maintenance. These systems can automatically adjust equipment operation, schedule maintenance activities, and even perform simple maintenance tasks without human intervention.
Digital Twin Technology Evolution
Digital twin technology continues to evolve toward more sophisticated and comprehensive virtual representations of physical assets. Advanced digital twins integrate multiple data sources and analytical techniques to provide unprecedented insights into equipment behavior and performance.
Physics-informed machine learning combines traditional engineering models with data-driven approaches to create more accurate and interpretable predictive models. These hybrid approaches leverage the strengths of both methodologies to improve prediction accuracy and reliability.
Virtual reality and augmented reality interfaces enable immersive interaction with digital twin models. Maintenance technicians can use these interfaces to visualize equipment conditions, explore failure scenarios, and plan maintenance activities more effectively.
Collaborative digital twins enable multiple stakeholders to interact with the same virtual asset simultaneously. This capability supports better communication and coordination between maintenance teams, operations staff, and engineering personnel.
Artificial Intelligence Advancement
By 2025, it is anticipated that more than 60% of new product introductions in the manufacturing sector will utilize generative AI for design and concept creation. Generative AI technologies are beginning to influence predictive maintenance through synthetic data generation and automated model development.
Explainable AI (XAI) technologies help maintenance teams understand how predictive models reach their conclusions. This transparency builds trust in AI systems and enables better integration with human decision-making processes.
Federated learning approaches enable predictive maintenance systems to learn from data across multiple facilities while protecting proprietary information. This collaborative learning model accelerates AI development and improves model performance.
Reinforcement learning applications in predictive maintenance enable systems to optimize maintenance strategies through trial and error. These approaches can discover novel maintenance strategies that traditional methods might not identify.
Building a Successful Implementation Roadmap
Strategic Planning and Assessment
Successful AI predictive maintenance implementations require comprehensive strategic planning that aligns technology capabilities with business objectives. Organizations must assess their current maintenance practices, identify improvement opportunities, and develop realistic implementation timelines.
Maturity assessment helps organizations understand their readiness for predictive maintenance implementation. This assessment should evaluate data availability, technical capabilities, organizational culture, and resource constraints that could affect implementation success.
Business case development requires careful analysis of costs, benefits, and risks associated with predictive maintenance implementation. Strong business cases include quantified benefits, realistic cost estimates, and risk mitigation strategies.
Stakeholder alignment ensures that all affected parties understand and support the predictive maintenance initiative. This alignment is critical for securing resources, managing change, and achieving implementation objectives.
Technology Selection and Integration
Technology selection decisions should consider current infrastructure, future requirements, and vendor capabilities. Organizations should evaluate solutions based on technical capabilities, integration requirements, scalability, and total cost of ownership.
Proof of concept projects enable organizations to evaluate technology options before making major commitments. These projects should focus on representative use cases that demonstrate key capabilities and potential value.
Integration planning must consider existing systems, data flows, and operational procedures. Comprehensive integration plans reduce implementation risks and ensure that new systems work effectively with existing infrastructure.
Vendor management strategies should address ongoing support requirements, system updates, and performance monitoring. Strong vendor relationships are essential for long-term success of predictive maintenance implementations.
Scaling and Continuous Improvement
Scaling strategies should consider lessons learned from pilot projects and early implementations. Successful scaling requires systematic approaches to technology deployment, change management, and performance optimization.
Performance monitoring systems track both technical and business metrics to ensure that predictive maintenance systems continue to deliver value. Regular performance reviews identify areas for improvement and optimization.
Continuous improvement processes ensure that predictive maintenance systems evolve and adapt to changing business requirements. These processes should include regular model updates, system enhancements, and capability expansions.
Innovation programs encourage exploration of new technologies and applications that can enhance predictive maintenance value. Organizations should maintain awareness of emerging technologies and evaluate their potential for improving maintenance operations.
Frequently Asked Questions
What is AI predictive maintenance and how does it work?
AI predictive maintenance uses machine learning algorithms to analyze sensor data from manufacturing equipment and predict when maintenance is needed. It works by identifying patterns in equipment behavior that indicate potential failures, enabling proactive maintenance before breakdowns occur.
How much can AI predictive maintenance reduce maintenance costs?
Organizations typically see 15-25% reduction in maintenance costs through AI predictive maintenance. Benefits include reduced emergency repairs, optimized parts inventory, and improved maintenance scheduling efficiency that collectively lower overall maintenance expenses.
What types of sensors are needed for predictive maintenance?
Common sensors include vibration sensors for rotating equipment, temperature sensors for thermal monitoring, acoustic sensors for sound analysis, and pressure sensors for fluid systems. The specific sensors needed depend on equipment types and failure modes being monitored.
How long does it take to implement AI predictive maintenance?
Implementation timelines vary from 3-12 months depending on project scope and complexity. Pilot projects typically take 3-6 months, while full-scale implementations across multiple facilities can take 12-18 months including training and change management.
What are the biggest challenges in implementing AI predictive maintenance?
Major challenges include data quality issues, integration complexity with existing systems, skills gaps in AI technology, cultural resistance to change, and cybersecurity concerns. Successful implementations address these challenges through careful planning and change management.
Can AI predictive maintenance work with older manufacturing equipment?
Yes, AI predictive maintenance can be retrofitted to older equipment through add-on sensors and wireless communication systems. However, integration may be more complex and expensive compared to newer equipment with built-in connectivity and sensors.
How accurate are AI predictive maintenance systems?
Modern AI predictive maintenance systems achieve 85-95% accuracy in predicting equipment failures. Accuracy depends on data quality, algorithm selection, and the specific application. Systems typically improve accuracy over time as they learn from more operational data.
What ROI can organizations expect from AI predictive maintenance?
Organizations typically achieve ROI of 300-500% over 3-5 years from AI predictive maintenance implementations. Returns come from reduced downtime, lower maintenance costs, improved equipment reliability, and enhanced production efficiency.
How does AI predictive maintenance integrate with existing CMMS systems?
AI predictive maintenance systems can integrate with existing CMMS through APIs and data interfaces. Integration enables automated work order generation, maintenance scheduling optimization, and comprehensive reporting that combines predictive insights with traditional maintenance management.
What skills are needed to manage AI predictive maintenance systems?
Key skills include data analysis, machine learning basics, industrial automation knowledge, and maintenance engineering expertise. Organizations often need to train existing staff or hire new talent with combined technical and operational capabilities.
How does cybersecurity affect AI predictive maintenance implementations?
Cybersecurity is critical for protecting sensitive operational data and preventing disruption of manufacturing operations. Implementations require network security, data encryption, access controls, and regular security assessments to maintain protection against cyber threats.
What is the future of AI in manufacturing maintenance?
The future includes edge computing for real-time processing, digital twin technology integration, autonomous maintenance systems, and advanced AI techniques like generative AI and explainable AI that will further enhance predictive maintenance capabilities and value.